What is 6s?
In lean manufacturing and organisational efficiency, the 6S methodology has emerged as a comprehensive approach to creating and maintaining a clean, organized and efficient workplace. This system extends on the traditional 5S framework by adding a crucial sixth element, “Safety”, to the mix. The 6S methodology has its roots in Japanese manufacturing practices. It is designed to enhance productivity, ensure safety and foster a culture of continuous improvement in workplaces across various industries. In this article we will explore the 6S methodology, its components, implementation strategies and the benefits it brings to organisations.
History and Foundations of 6S
As mentioned before the 6s has its roots from 5S methodology, which originated in Japan and became a cornerstone of lean manufacturing practices. The original 5S framework focuses on Sort (Seiri), Set in Order (Seiton), Shine (Seiso), Standardize (Seiketsu), and Sustain (Shitsuke). The addition of Safety (Safety) transforms 5S into 6S, emphasizing the importance of a safe working environment as an integral part of organizational efficiency and effectiveness.
The Six Pillars of 6S are:
Sort (Seiri): This step involves sorting through items in the workplace and keeping only what is necessary for the tasks at hand. Unnecessary items are removed, reducing clutter and freeing up space.
Set in Order (Seiton): After sorting, the next step is to organize and arrange tools, materials, and information in an orderly manner. Everything should have its place, and everything should be in its place, making it easy for employees to find what they need without wasting time.
Shine (Seiso): This phase focuses on cleaning the workplace and ensuring that equipment and tools are maintained in good condition. Regular cleaning prevents the buildup of dirt and grime, which can lead to equipment failure and health hazards.
Standardize (Seiketsu): Standardization involves developing work practices that are consistent and repeatable. This includes creating schedules, checklists, and procedures to ensure that the first three S’s are carried out consistently across the organization.
Sustain (Shitsuke): The fifth S is about sustaining the gains made from implementing the first four steps. This involves training, discipline, and the development of a culture that values continuous improvement and adherence to established practices.
Safety: The addition of Safety to the traditional 5S methodology underscores the importance of creating a safe working environment. This involves identifying potential hazards, implementing safety measures and fostering a safety culture where safety is everyone’s responsibility.
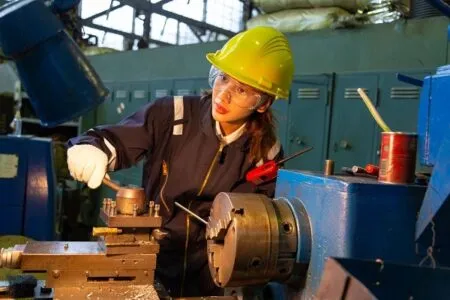
Implementing 6S in the Workplace
Implementing 6S requires commitment from all levels of an organisation, from top management to frontline employees. The process typically involves the following steps:
Education and Training: Educating employees about the principles of 6S and training them on its implementation is the first step. This ensures everyone understands the value of 6S and their role in maintaining it. Creating an online induction course might assist in achieving this goal.
Assessment and Planning: Conduct an initial assessment of the current state of the workplace. This involves identifying areas for improvement and planning how the 6S principles can be applied.
Execution: Begin implementing the 6S steps, starting with Sort and progressing through to Safety. This phase is hands-on and requires active participation from all team members.
Evaluation and Improvement: After implementing the 6S steps, evaluate the results. Identify areas for improvement and make adjustments as necessary. The goal is continuous improvement, so this process is ongoing.
Benefits of 6S
The implementation of 6S brings numerous benefits to organisations, including but not limited to:
- Increased Efficiency: By reducing clutter and improving organisation, 6S helps streamline operations, making it easier for employees to perform their tasks efficiently.
- Enhanced Safety: The emphasis on safety reduces the risk of accidents and injuries, creating a safer workplace for everyone.
- Improved Productivity: With a well-organised and clean workplace, employees can focus on their tasks without distractions, leading to improved productivity.
- Higher Quality: Standardised processes and a focus on continuous improvement contribute to higher quality products and services.
- Employee Satisfaction: A clean, organized and safe workplace improves employee morale and satisfaction, leading to lower turnover and higher engagement.
Challenges and Considerations
While the benefits of 6S are significant, organisations may still face challenges in its implementation. Resistance to change, lack of management support and insufficient training can hinder the successful adoption of 6S practices. To overcome these challenges, it is crucial for organisations to foster a culture of continuous improvement, provide ongoing training and support, and engage employees at all levels in the process.
The 6S methodology represents an evolution in lean manufacturing and workplace efficiency, extending beyond mere organisation and cleanliness to incorporate safety as a fundamental component. By embracing the principles of 6S, organisations can create a safer, more efficient and more productive work environment.
However, the success of 6S depends on a sustained commitment to continuous improvement and the active participation of everyone in the organization. As businesses continue to navigate the complexities of modern industry, the principles of 6S offer a proven framework for enhancing performance and achieving operational excellence.