Machine safety is critical to maintaining a safe workplace, particularly in industries that rely heavily on machinery. In Australia, safeguarding workers from machine-related injuries is governed by various workplace health and safety (WHS) laws and standards. Compliance with the Work Health and Safety Act 2011 (WHS Act), Work Health and Safety Regulations 2011 (WHS Regulations), and relevant Australian Standards, such as AS 4024.1 – 2019 for machinery safety, is essential for employers. In this article we are going to discuss best practices for machine safety and guarding that align with these regulations, ensuring the protection of workers while maintaining productivity.
Understanding the Importance of Machine Guarding
Machine guarding is designed to protect workers from hazardous mechanical parts and prevent accidents. In Australia, under the WHS Act, employers are legally obligated to ensure the health and safety of their employees, which includes safeguarding workers from hazardous machinery. Section 19 of the WHS Act outlines the primary duty of care, which includes eliminating or minimising risks posed by machinery.
The risks associated with unguarded machinery, such as entanglement, crushing and shearing, make machine guards vital to preventing serious workplace injuries. The WHS Regulations specify that where there is a risk of injury from machinery, guards must be installed to protect workers from hazardous parts.
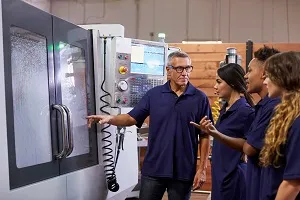
Types of Machine Guards
The WHS Regulations and AS 4024.1 – 2019 outline various types of guards, each suited to different machines and hazards:
- Fixed Guards: Permanent barriers, these guards are ideal for areas where access to moving parts is not required during normal operation.
- Interlocking Guards: These guards are designed to stop machine operation when the guard is opened, protecting workers during maintenance or repair.
- Adjustable Guards: Manually adjustable, these guards are used for machines that handle materials of different sizes.
- Self-Adjusting Guards: Common on tools like saws, these guards move according to the size and shape of the material being processed.
To comply with Australian regulations, all guards must be robust, properly installed and maintained to ensure worker protection.
Best Practices for Machine Safety and Guarding
To prevent injuries and ensure compliance with the WHS Act and WHS Regulations, employers should adopt several best practices for machine safety and guarding:
a. Conducting Risk Assessments
Under Part 3.1 of the WHS Regulations, employers must identify and assess risks associated with machinery. A risk assessment determines which parts of the machine pose the greatest danger and which safeguards are necessary to mitigate those risks. According to AS 4024.1 – 2019, this involves analyzing the machine’s operations, material handling processes and the likelihood of accidents.
Risk assessments should be carried out by qualified personnel who are familiar with the machinery, its hazards and safety regulations. This ensures a tailored safety plan that meets the specific needs of each machine.
b. Proper Installation and Maintenance of Guards
Once risks are identified, installing appropriate machine guards is essential. The WHS Regulations require employers to ensure that all guards are correctly installed and maintained. The following steps ensure compliance:
- Install guards according to the manufacturer’s instructions and ensure they cover all hazardous parts.
- Regularly inspect guards for wear, damage, or signs of tampering.
- Replace any damaged guards immediately.
- Ensure that guards are securely attached and cannot be easily removed or bypassed by workers.
By maintaining guards according to AS 4024.1, businesses can reduce the risk of machinery-related injuries and remain compliant with WHS requirements.
c. Training and Education
Section 19 of the WHS Act requires that employers provide information, training, instruction and supervision to ensure that workers can operate machinery safely. Training should focus on:
- Safe machine operation and the role of machine guards.
- Identifying hazards related to the machine, such as exposed parts or malfunctioning guards.
- Procedures for safe machine shutdown and startup.
- The correct use of personal protective equipment (PPE).
Regular training sessions should be conducted, especially when new machinery is introduced or safety protocols are updated. Workers must also understand their responsibility to report any safety concerns or issues with machine guards.
d. Lockout/Tagout (LOTO) Procedures
Australian WHS regulations emphasize the importance of Lockout/Tagout (LOTO) procedures, particularly during maintenance, repair, or when guards need to be removed. LOTO procedures are designed to prevent accidental machine start-up while a worker is in a dangerous position. The process involves:
- Isolating the machine from its energy source.
- Locking the machine to ensure it cannot be re-energized until work is complete.
- Attaching a tag to indicate that maintenance is being carried out.
- Testing to ensure the machine is fully de-energized before work begins.
Following LOTO procedures as outlined in AS 4024.1 ensures worker safety during repairs and maintenance and helps businesses comply with Australian safety laws.
e. Continuous Monitoring and Improvement
Maintaining machine safety requires regular monitoring and continuous improvement. Employers must conduct regular safety audits and machine inspections to ensure that guards are functioning correctly and that workers are following safety procedures. Feedback from workers is invaluable for identifying hazards or issues that might otherwise go unnoticed.
By fostering a safety culture where employees are encouraged to report concerns, businesses can continuously improve their safety protocols and stay ahead of potential hazards. Regular updates to risk assessments and safety measures also help businesses stay compliant with changes in Australian safety regulations.
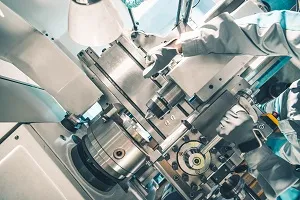
Compliance with Australian Safety Regulations
Compliance with Australian safety regulations, such as the WHS Act, WHS Regulations and relevant Australian Standards is not optional. Failure to comply can lead to severe penalties, including fines and business shutdowns. Employers must familiarise themselves with the specific requirements outlined in:
- WHS Act 2011: Establishes the legal framework for workplace safety, including the duty of care to eliminate or minimize risks.
- WHS Regulations 2011: Provides detailed guidelines on risk management, machinery safety, and the use of guards.
- AS 4024.1 – 2019: The Australian Standard for safeguarding machinery, which provides detailed information on guard requirements, machine safety procedures, and risk assessments.
Employers are also required to stay updated on changes to legislation and ensure that all machinery meets current safety standards.
The Role of Technology in Machine Safety
Advancements in technology are helping Australian businesses improve machine safety. Devices such as safety sensors, light curtains and interlocking devices offer additional layers of protection. For example:
- Safety Sensors: These sensors detect when a worker is too close to dangerous machine parts and stop the machine automatically.
- Light Curtains: These create an invisible barrier around hazardous areas. If the barrier is breached, the machine stops.
- Interlocking Devices: Prevent machines from starting unless all guards are securely in place.
By incorporating these technologies, businesses can enhance their machine safety practices and reduce the likelihood of workplace injuries.
Final Words
Machine safety and guarding are essential components of workplace safety in Australia, governed by the WHS Act, WHS Regulations, and Australian Standards like AS 4024.1. By conducting thorough risk assessments, installing appropriate guards, providing regular training, and complying with Lockout/Tagout procedures, businesses can significantly reduce the risk of machine-related injuries.
Continuous monitoring and adopting new technologies further enhance safety protocols. Compliance with these laws not only protects workers but also ensures that businesses operate within the legal framework established by Australian workplace safety legislation.