Safety at work
There are numerous reasons why you should take safety at work seriously. In 2018, a total of 144 workers were fatally injured at work in Australia. This translated to a fatality rate of 1.1 for every 100,000 workers. While this is a 62% drop from a peak rate of 3.0 per 100,000 workers in 2007, these figures can be reduced even further.
Workplace safety is more than a list of actions focused on preventing accidents. Rather, it should be woven into your company’s vision, mission, policies and procedures. This is an effective way of demonstrating its importance to everyone across your company.
How to Create a Safety Culture at the Workplace
The four steps that will be the starting point towards promoting a safety culture in your organisation are:
- Risk evaluation
- Designing a safety plan
- Implementing your safety plan
- Monitoring, evaluating and improving your safety plan
1. Risk Evaluation
Also referred to as risk assessment, risk evaluation refers to a systematic examination of the workplace so that:
- Risks or hazards are identified
- The likelihood and severity of the identified risks are assessed
- Measures that will reduce or control these risks can be put in place
Apart from ensuring that your company complies with existing legislative requirements, evaluating risks improves the overall safety of your employees.
Risk assessment should not be confused with hazard or job safety analysis. The main difference between the two is the scope they cover. A job safety or job hazard analysis is normally performed on a single task and it focuses on job-specific risks. On the other hand, risk assessments are normally performed across the entire workplace.
Risk evaluation should be carried out by people who are experienced in assessing hazards, their likelihood, severity, and control measures. You should plan for a risk evaluation procedure every time you introduce a new procedure, substance or a machine that could lead to new hazards. While risks or hazards are dissimilar depending on the industry or company, there are four general steps organisations use to assess risks. They include:
- STEP 1: Hazard identification
Safe Work Australia demands that employers assess all health and safety risks that their workers face. Workplace hazards can be classified as follows:
- Physical hazards
Despite their name, these hazards are oftentimes the least obvious. Physical hazards refer to anything in the workplace which can cause bodily harm to the workers. Examples include slips and falls, falls from heights, lifting, injuries from machinery, dust, noise, awkward postures, and so on
- Chemical hazards
These are risks involved with the use of chemicals. Some of the most common chemicals in workplaces include; acids, cleaning products, caustic substances, glues, pesticides, paints, petroleum products, and solvents. Health hazards are normally due to chemical absorption, inhalation, ingestion, and swallowing. These hazards can result in acid burns, asphyxiation, nausea and vomiting (immediate symptoms) or asthma, cancer, dermatitis and liver damage (after prolonged exposure).
- Biological hazards
Biological hazards are those that result from working with animals, infectious plants and people. They may include exposure to bacteria and viruses, insect bites, blood and body fluids, mould and vermin among others.
- Ergonomic hazards
Ergonomic hazards are those that result in musculoskeletal injuries. They may be caused by awkward movements, repetitive movements, poor lighting and poor posture.
- Psychosocial hazards
These are hazards that could have adverse effects on your employees’ mental health. They may include stress, sexual harassment, victimisation, and violence in the workplace.
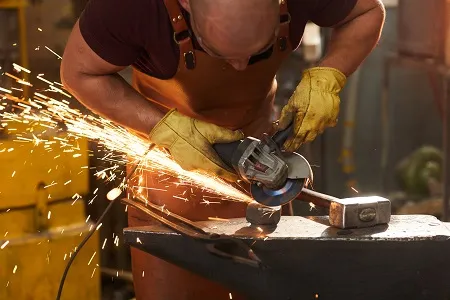
- STEP 2: Deciding who and what is in harm’s way and how they could be harmed
After identifying hazards, you need to determine which assets would be negatively affected if the hazard happened. Assets that may be deemed at risk include your employees, business operations, critical infrastructure, IT systems, and company reputation.
- STEP 3: Putting in place control measures
Carrying out a risk analysis exercise helps identify how hazards will impact your organisation and the likely measures that could minimise or eliminate the hazard’s effect on business assets. Potential hazards may include employee injuries or even loss of life, property damage, financial loss, business interruption and legal penalties. The control measures should be reasonably practicable and remain effective over time.
Even after all control measures have been implemented, some risk will remain. You will have to decide for whether the risk remains high, medium or low and what must be done.
- STEP 4: Reviewing your risk assessment
In modern business environments, risks and the resulting controls are subject to change. You must review your risk assessment regularly to ensure that you accommodate these changes.
2. Designing a Safety Plan
Accidents at the workplace not only affect the injured person but they also have an impact on your business. This could be in terms of lost productivity, increased out-of-pocket expenses, higher insurance premiums and in some cases, lawsuits.
Organisations can protect themselves as well as their employees by adopting a proactive approach towards workplace safety. Investing in a workplace safety program improves the company’s bottom line. But how do you go about this?
1. Get everyone involved
For a workplace safety program to be effective everyone, from the top managers to the least employee needs to be committed. The management needs to clearly outline the organisation’s safety goals and communicate them to the employees. They also need to set the model example for their employees to follow.
2. Training and education
Some organisations make the mistake of only training their employees as and when they are recruiting them. However, training and induction should not only be held during when a new employee is being oriented but it should be reinforced routinely. Training sessions should be scheduled whenever new equipment, processes or procedures are introduced. Such sessions should cover topics such as how to identify new hazards, prevent accidents and safety-related incidents and respond to injuries.
Organisations should also issue employee handbooks to workers. Also, posters and materials explaining workplace safety processes and procedures as well as fair employment practices should be printed and placed in strategic positions. Posters act as constant reminders of the workplace safety rules. They should be displayed in places that are accessible and visible to all employees.
3. Enforcing and continuous evaluation
The management needs to be vigilant and stress on the need for each employee to follow the pre-determined safety policies and procedures. WHS could fine your organisation significant amounts of money if they establish that there are for safety violations. Being proactive rather than reactive when it comes to enforcement of safety laws and procedures is a viable cost-control measure.
Routine safety audits, meetings and annual training sessions are effective ways of enforcing workplace safety rules. Managers must also ensure that the safety programs in place are evaluated annually or whenever previously unknown or new risks and hazards are discovered.
By focusing on injury prevention by enforcing rules that require employees at all levels to adhere to safety standards, businesses can keep their most important assets safe and contribute to long-term business success.
3. Implementing the Safety Plan
Rather than being perceived as a priority, a safety culture should be entrenched into the very fabric of every workplace. It should start at the executive level and channelled down through leadership teams in each department.
Apart from the senior management, safety at the workplace touches other departments in several ways:
- The human resources department
Every safety violation or safety-related incidents should be documented by the human resource department. HR leadership plays a key role in creating a culture of safety in the workplace.
- Accounting
Each department needs to include safety in its operating budget. The accounting department needs to include safety-related expenses in the overall budget and as well as set aside money related to safety training and related activities.
- Legal
Safety violations and workplace injuries involve the legal departments. Even minor workplace injuries could result in lawsuits that may not only require costly counsel but also take months or even years to resolve. Even though your organization may not be at fault, legal fees can quickly drain your profits. The legal department should also stay updated on workplace safety laws and regulations. The department’s role in creating a safe workplace cannot be ignored.
- Procurement
Getting the right safety products such as PPE, helmets, signage, and so on at the best price and ensuring that these products are available to employees is essential for an effective safety program. Also, due to their position in the supply chain, persons in the purchasing department have the most recent information on new or upcoming safety products.
4. Monitoring, Evaluating and Improving Your Safety Plan
Your organisation must keep tabs on the frequency of workplace injuries as well as their severity. Near-misses are a perfect opportunity to identify potential hazards and find a way of improving your workplace’s safety plan. Managers and employees should perceive incident investigations as a process of improving safety practices and not a fault-finding mission.
Constantly revamping your safety plan is a huge investment, but one that will pay off by minimizing the number of workplace accidents.
How to Use Induct for Work as a Tool to Enhance Workplace Safety
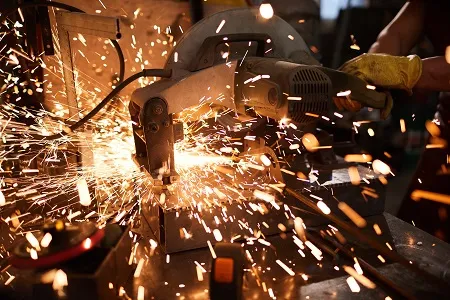
Induct for Work is an intuitive online induction tool that has businesses and organisations put an effective training and induction system in place.
Being purely an online induction and compliance training tool, Induct for Work has helped streamline operational efficiencies. Our clients report notable drops in lost production times.
This because there is no need for trainers or managers required to deliver face-to-face inductions. Rather, the online format allows for induction and other safety training courses to run as and when they are needed. This means new, existing employees and contractors can complete their induction course at their own convenience as long as they are connected to the internet. For instance, to avoid the loss of working hours on existing employees or having to assign someone to oversee the training, online inductions can be completed after working hours or from home.
When using Induct for Work, you will be able to classify your induction content into different groups. For instance, you can develop different safety training content meant for employees, casuals contractors and even visitors. We have templates meant for each group to allow for rapid inductions.
Induct for Work provides you with proof of meeting compliance requirements. This is because the platform will:
- Record engagement dates
- Capture the inductees’ acknowledgement of safety policies, procedures, and induction courses
- Show when materials were read
- Keep track of assessment scores and attempts
- Record evidence of external training, dates and verifications
- Schedule refresher training
- Collect documents such as work permits, licenses and insurance documents among other work-related documentation from employees and contractors. You will also be notified should any of these documents fall due for renewal.
You probably know that traditional induction training has a potential flaw of being inconsistent, especially when it comes to the messages the learners receive. This is because this form of training relies heavily on the trainer’s experience and their tone when conducting the training. This flaw is magnified when there’s more than one person conducting induction and safety training sessions. By Induct for Works, you are guaranteed that every person that signs up for the training will receive the same information each time, regardless of when or where their induction training is completed.
As far as learning and information retention is concerned, we are different. Some of us learn best through reading, while others prefer audios and visuals. Induct for Work accommodates all these learning styles, thus allowing your inductees to absorb and retain information in their own way. You can use online assessments to identify any knowledge gaps so that every person is adequately trained. This also helps you maintain your compliance standards.
Induct for Work has a user-friendly and intuitive interface complete with administration capabilities. As an administrator, you will be able to add, track and manage inductee profiles. By migrating your induction processes online, you will save on costs associated with outdated training such as travel and accommodation, trainer hire, printed materials, room space and reduced employee productivity are eliminated.
Do you have any questions or great tips to share?
Induct for Work – the only online induction system you would need to run online inductions.