What short safety topics to cover during your toolbox meetings
Safe Work Australia requires employers to make employee safety and well-being their priority. But how do you keep your employees from forgetting the safety processes and procedures they learnt from the project’s onset? Holding regular safety briefings or toolbox talks is an effective way of providing additional safety training. Such briefings also keep the employees abreast of changing policies as far as safety at the workplace is concerned.
Defining a toolbox meeting
Also referred to as tailgate meetings or safety briefings, toolbox meetings are informal safety meetings that are mostly held before the beginning of a shift. They are a great way of:
- Reinforcing workplace safety basics
- Inform employees and contractors on changes in the working conditions, or even the job site, that might have taken place since the last shift
- Focusing on high-risk scenarios or accidents that might have occurred and how they could have been and will be prevented
While the idea behind such safety briefings can be traced back to the construction industry, any organisation that values the safety of its employees should hold them regularly. Details of the briefings should be recorded and filed away. It’s important to record the dates when such meetings took place, the agenda, and the attendees.
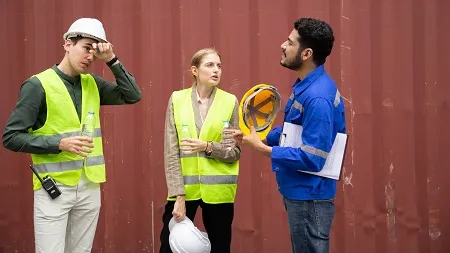
What safety topics should be covered in a toolbox meeting or talk?
While the core topics that should be covered in a safety briefing may vary from industry to industry, there are a few topics that cut across the board. They include:
- Basic workplace safety
No matter how many safety training seminars or guidelines you set in place, they will not be effective if your employees and contractors are not invested in following them. In a toolbox meeting, you will need to cover basic workplace safety practices such as:
- The need to wear personal protective equipment (PPE)
Whether it is something simple as putting on earplugs or something as huge as a chemical suit, PPEs are mean to protect the wearer against physical harm or hazards that the workplace presents. Cover the basics on the importance of wearing PPE.
- Why they should never take shortcuts
Workplace policies and procedures exist to keep the employees, contractors and visitors to the job site safe. During a toolbox meeting, sensitize on the need for employees and contractors to use each tool and machine according to the given instructions.
- The need to keep emergency exits clear
While this seems like a no-brainer, emphasize the need to ensure that trolley carts, forklifts, ladders, and so on do not block emergency exits. Paths leading to emergency equipment shutoffs need to be left clear in case any equipment needs to be powered down urgently.
- Making them aware of their surroundings
Each workplace presents inherent hazards. By being aware of potential hazards and knowing their surroundings, employees and contractors are able to avoid unnecessary workplace injuries. Emphasize the need for people to communicate should they identify a potential hazard.
- Office safety
In an office environment, incidents and injuries such as eye strain, back pain and so on are perceived as a normal or an expected part of the working process. Therefore, most workplaces fail to adopt ergonomic changes that will keep employees safe and productive. Your safety briefing should include the need to:
- Adopt the right posture
- How to lift and carry items to prevent back injuries
- The need to keep workspaces clutter-free
- Electrical and fire safety practices
- Equipment safety
Observing the right equipment safety procedures is important not only to the operators but also to other personnel and visitors. When it comes to equipment safety briefings, some of the topics you should cover include:-
- Load limits
Operators should be aware of the different load limits for the various machines they’ll be using throughout the day. They should also ensure that the loads are secured with the correct rigging attachments. Remind workers on the safe distances they should observe and maintain when loading or unloading is taking place.
- Machine maintenance and inspections
Before commencing with any task, machine operators should ensure that perform walk-around inspections. This should be done using a pre-developed list of machine parts and components where they check off those that are in good working condition. A report should be submitted to the safety department before the machine is powered up. Machine operators should be reminded of the need to ensure that their machines and equipment are maintained and inspected regularly.
- Blind spots
Emphasize on the need for operators to be sure that there’s no one behind them or in blind spots when operating a machine. Workers in places where machines are being used should always wear high visibility vests.
- Machine operation practices and procedures
When operating heavy equipment and machinery, ask them to always wear seatbelts. Ask them to observe proper mounting and dismounting procedures. Machine operators should be in communication with those working around them. Two-way radios are the best option. If these are not available, there should be a properly trained spotter.
Stress on the need for operators to ensure that machines are operated at the recommended speeds. They should be controlled in a manner that is consistent with the job requirements. Equipment should never be left unattended if the motor is running. Ask personnel to shut off machines and avoid smoking during refuelling. Loose clothing should never be worn by those working around machines and equipment as they can get caught by moving parts.
Keep in mind that each workplace is unique, therefore, ensure the topics in your safety briefing are relevant to you.
- Chemical safety
When the term ‘chemical’ is mentioned, most people tend to think of scientists working in laboratories. However, bug sprays, cleaning solvents including bleach, disinfectants, and mildew removers glues, paints, lubricants, copier chemicals, fuels, fertilizers lawn chemicals among others are chemicals. In your safety briefing, include such chemical safety topics as:-
- Spill response
- Storeroom safety
- Housekeeping
- Airflow while using chemicals
- Emergency response should someone come into contact with a chemical
During your toolbox meeting emphasize on the need for workers to read the label or refer to Material Safety Data Sheets (MSDSs) before using any chemical.
Every workplace has its own unique challenges as far as chemical exposure is concerned. Planning for any identified hazards and addressing them in your safety briefing will help ensure a safe workplace.
- Weather-related safety
Safety briefings need to be related to the existing weather conditions. For instance, you can advise employees on the need to stay hydrated during the summer especially when working outdoors, how to prevent heatstroke and skin cancer. If it’s during the winter, cover such topics as signs of hypothermia and how to drive safely in the snow.
How to communicate effectively during safety briefings
These are some of the ways you can ensure the message in your safety briefing gets home:
- Keep it brief -
no matter how important the topic of the meeting is, your audience’s attention span is rather limited. Keeping in mind that safety briefings should be brief, go straight to the point and put any additional information in a handout. In future meetings, build on the same topic by adding relevant or new content to keep it interesting. Use short and straightforward phrases and avoid jargon or slang.
- Be relevant -
the content in your safety briefings should be relevant to the job site or industry. It should make them feel safe on and off the job. If employees do not feel that the topics in your safety briefings do not apply to them, they are likely to tune out or lose interest.
- Be careful with the delivery pace -
rushing through a safety briefing only defeats its purpose. This is because you’ll come across as impatient or not interested in the audience’s questions or opinions. Also, by delivering the message too slowly, you risk losing the audience’s interest. You will need to strike a balance between the two.
- Maintain a positive attitude -
unlike incident investigations that are a reactive approach towards workplace safety, safety talks are a proactive approach to encourage safe behaviour. Therefore, you should focus on what should be done to create a healthy and safe work environment rather than discussing what has gone wrong in the past.
- Make your safety briefing sessions interactive -
one way of making sure that your audience pays attention is by making your toolbox meetings interactive as opposed to lecture sessions. Demonstrations and role-playing not only give your audience a chance to participate but also helps them retain the information they learn. This approach also helps the audience perceive safety briefings as something positive as opposed to something they have to tolerate.
- Avoid statistics. Tell stories -
although people believe statistics, they are more likely to remember stories. Your audience is likely to identify with the story and keep it at the top of their minds. This is the ultimate goal of any safety briefing. However, the stories you tell should also follow the above guidelines – they should be brief, relevant, and demonstrate the point clearly.
During your safety briefings, use open questions to evaluate your audience’s level of comprehension. Asking questions such as “do you understand” prompts your audience to answer “yes” even though they may not have understood.
The role of Induct for Work in safety briefings
Induct for Work is an online safety training platform that could help you effectively deliver your toolbox meeting content. Some of the ways Induct for Work benefits you when you’re delivering safety briefings include:
1. It saves you time
Safety briefings should be short and precise. Delivering your safety briefings online enables you to deliver a precise and concise message across the board. Through Induct for Work, you can generate individual-centric and engaging safety briefing content. You can send the safety briefing invite to the people who should take it before they set foot to your job site.
2. It allows you to deliver relevant content through templates
With conventional safety meetings, there’s a chance that you’ll get it wrong. If this happens, you have to keep retraining your staff to correct what you failed to communicate effectively in the first place.
What really matters when it comes to safety briefings is the delivery method. Safety or toolbox meetings should focus on specific personnel and what they need to know. Induct for Work provides you with industry-specific templates that include relevant policies, procedures and work norms. Using templates prevents you from getting sidetracked.
3. It puts the learners in control
It is a proven fact that adult learners prefer being in control of any training process. Providing online safety briefings online provides learners with ease of access to the content on-site or even before. The learners can work through the content at their pace and repeat the parts they do not understand as long as they complete the briefing in time.
4. It reduces your operational costs
Rather than involving department heads and safety officers in the safety briefings, Induct for Work enabled your employees to access the safety briefing content through their phone or personal computer. The platform also keeps track of the details of those who participate in the safety briefing. Apart from helping you keep proper records, this also helps you keep compliant with existing laws.
5. Your toolbox meetings will be more convenient
Toolbox or safety briefings are supposed to be held regularly. While most workplaces hold them weekly or even daily, you might want to hold them more regularly if your workplace has a high rotation of workers and contractors. Depending on the nature of your work-site, Induct for Work provides you with an agenda and enables you to gauge the workers’ and contractors’ comprehension levels. You can create a forum where learners provide feedback and ask questions.
Toolbox meetings and safety briefings are a critical part of building a strong safety culture. They also reinforce your organisation’s commitment towards protecting your employees. Holding regular safety briefings prevents the employees and the contractors in your job site from getting complacent when it comes to their safety and well-being.
Do you have any questions or great tips to share?
Induct for Work – the only online induction system you would need to run online inductions.